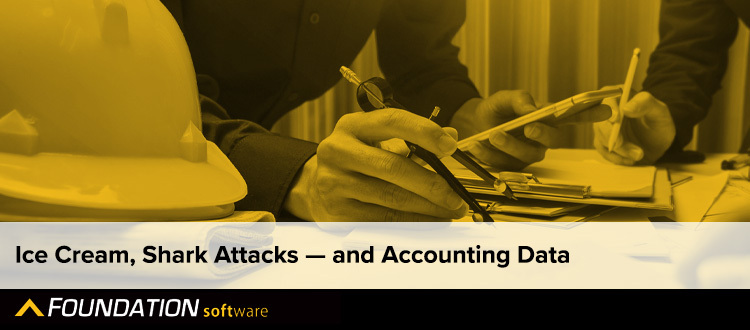
Guest Contributor: Kevin Bright, ProNovos
Ferreting out the difference between correlation and causation is important whenever you’re making decisions based on interrelated information.
Shark attacks, for example, are strongly correlated with higher ice cream sales, but it doesn’t take a statistician to wonder if something’s fishy here. The missing variable, of course, is the hot summer, which makes for more swimmers in the water, longer ice cream lines and a higher rate of run-ins with aquatic predators.
In the same way, those who gauge project performance using accounting data can benefit by thinking carefully about the relationships between different variables.
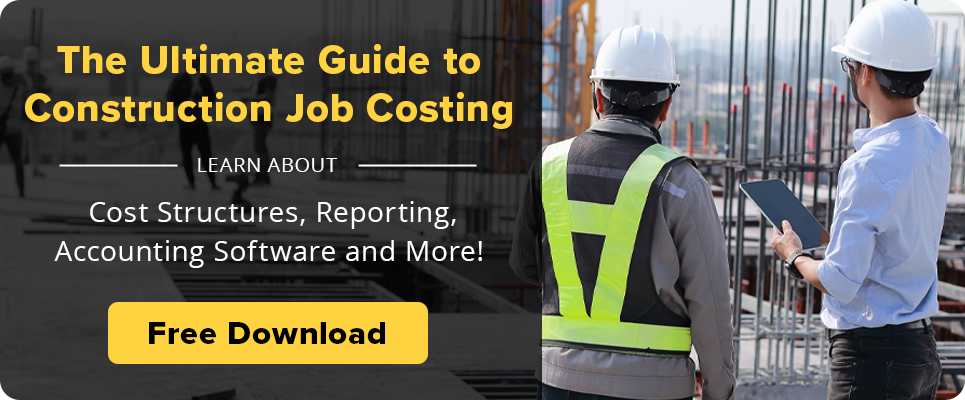
Labor-cost overruns, for instance, often merit an especially close look, particularly for subcontractors and companies that do a lot of self-performed work. According to a 2023 PlanGrid and FMI report, construction professionals spend an average of 35% of their time on non-productive activities, including looking for project information and resolving conflicts, directly impacting labor costs.
Confronted with spiraling labor costs, the first impulse of a project manager or other decision-maker could be to ask what the crews and superintendent could be “doing wrong.”
But, in reality, those avenues often should be explored last. Poor motivation among field personnel is rarely the root cause of busted labor budgets.
Rather, unexpected labor costs tend to be a sign of other problems. For example, flaws in the materials buyout could result in the wrong materials being shipped to that jobsite or materials arriving much later than expected. The project’s labor costs will naturally reflect those unforeseen delays.
Likewise, gaps in information-management can have a mushrooming effect on labor costs. Even the best architects and engineers sometimes omit details from their plans. If the contractor’s process for handling the resulting RFIs and submittals is cumbersome, then this, too, will translate into labor-cost overruns.
You could say the same about the effects of poor equipment-management, miscommunication among different trades or disconnects between the office and the field.
Watch for Warnings
So how can contractors quickly identify such root causes? Look for early warning signs within your labor data. Let’s say an activity on the job will run for two months. Once you have a week or two of data in hand, you can run an extrapolation to determine how your budget is shaping up. If the numbers aren’t good, it may be time to huddle with field personnel, ask about mitigating circumstances and start investigating the source of any erosion in labor productivity.
If you’re using an analytics dashboard to view your information, another option is to use drill paths to see what’s happening in more granular detail. This is where you click the different fields in the dashboard to see the data streams that go into individual calculations.
For the previous example of a flawed materials buyout, it’s important to be bought out as early as possible on any new activity. If you use a drilldown to go into your data and notice your materials costs for that new activity are $0, you’re clearly at risk of running late. The earlier you can spot such red flags, the better.
Not that flaws are always easy to see. On larger projects, job budgets will contain hundreds or thousands of items. Having access to tools like construction data analytics can allow you to create quick visualizations that highlight various Key Performance Indicators (KPIs). That’s important, because sometimes it’s not a giant flaw that skews the labor budget — it’s the cumulative effect of smaller inefficiencies. Visualizations allow you to identify and address each of these in order of importance.
Support the Field
As a general rule, if the superintendent is calling to ask for more information, describe missing equipment or otherwise call attention to something that’s gone wrong, you’re already too late in giving your crews the support they need.
That’s why it’s important to proactively communicate with superintendents. There’s a big difference between calling the super and saying, “Why is it taking so long?” and routinely saying to that person, “My job is to support you. What do you need from me?”
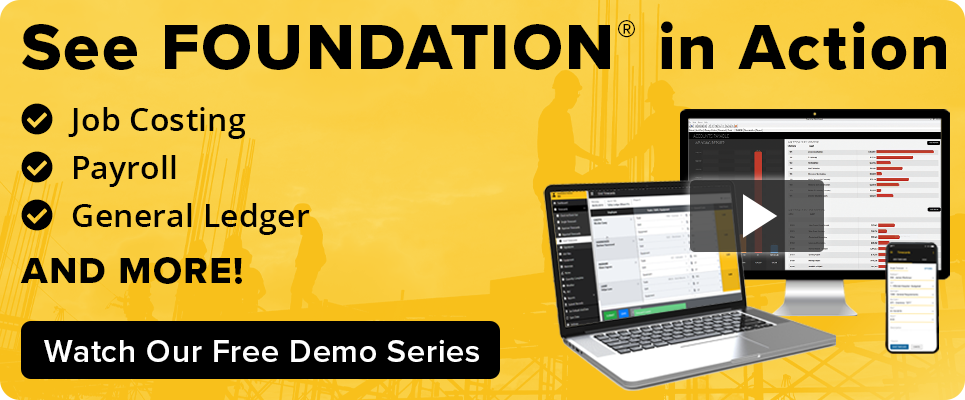
Cloud-based analytics and project-management platforms can reinforce such efforts. They give field personnel quick access to reports, drawings, photos, checklists, revisions, and other relevant project information. Office personnel, meanwhile, can integrate data from their accounting platform and other applications to create automated, custom reports that deliver higher-order insights and performance.
While tech tools and procedural best practices can be incredibly helpful, the most important factor is critical thinking — pausing to examine the relationships between the people, things and information that go into every construction project.
Share Article
Keep on current news in the construction industry. Subscribe to free eNews!
Our Top 3 YouTube Videos
Learn about our software more in depth with product overviews, demos, and much more!
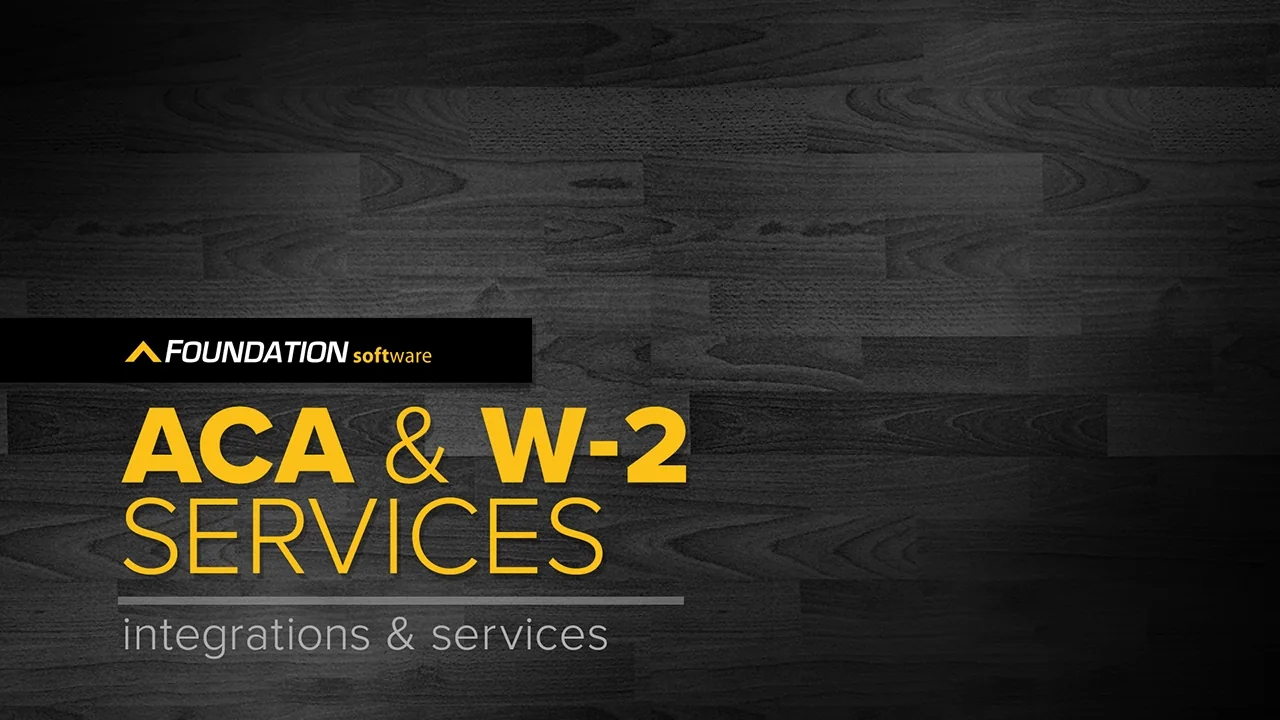
Our ACA reporting & e-filing services include official 1094-C and 1095-C IRS reporting, optional e-filing (no applying for a TCC code required), mailing to your employees and experienced support to help you.
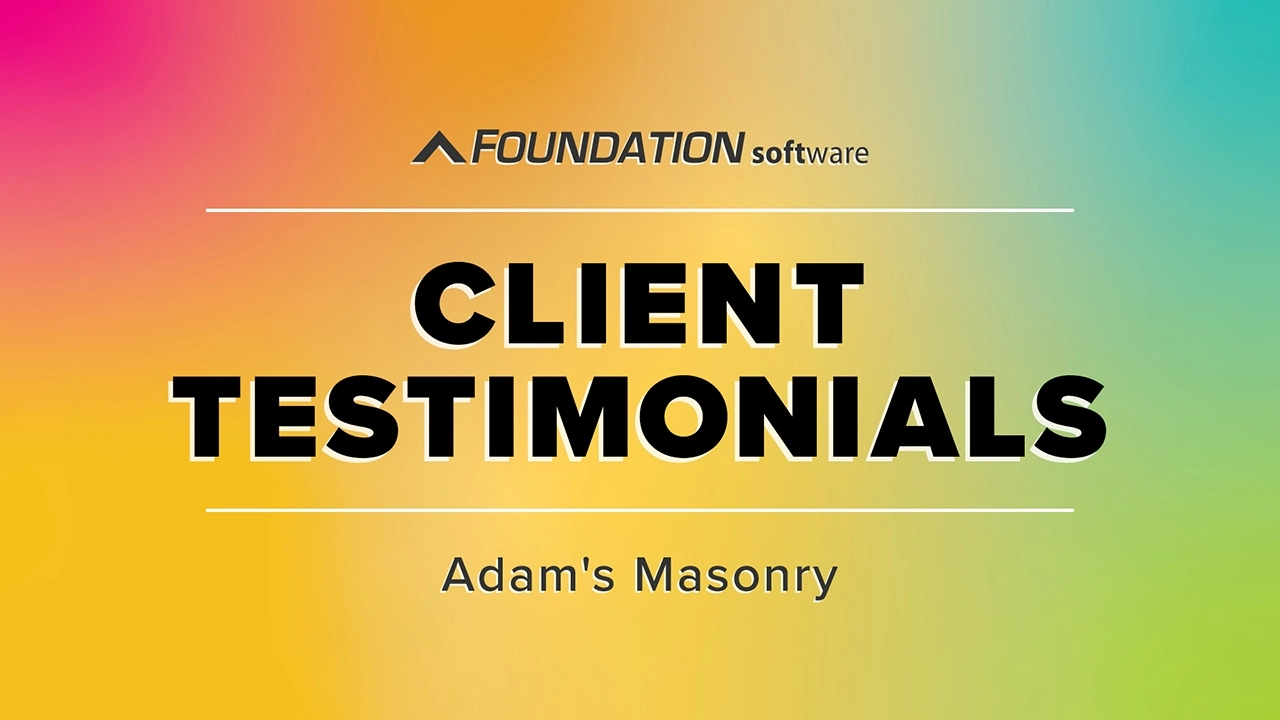
There are plenty of reasons to make FOUNDATION your choice for job cost accounting and construction management software — just ask our clients!
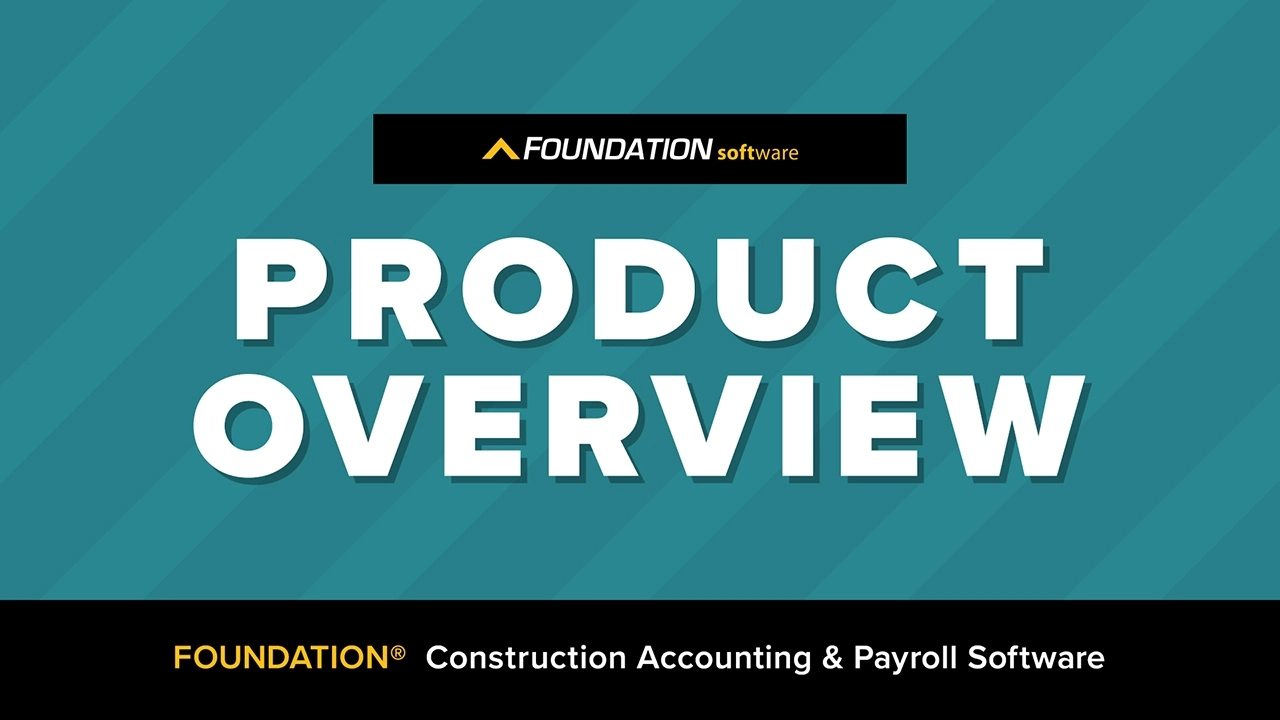
From job cost accounting software, to construction-specific payroll. Get an overview on your next all-in-one back-office solution.