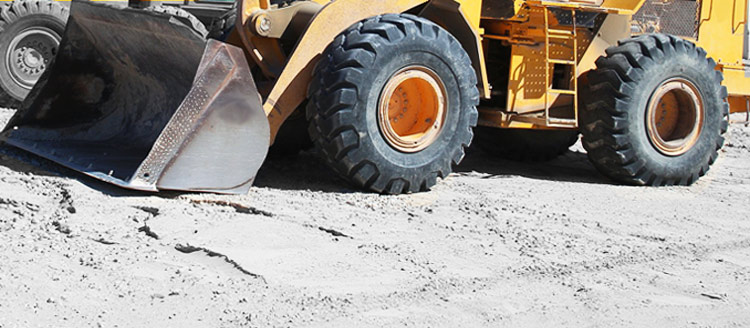
Construction equipment represents one of the largest investments a contractor can make. For example, if heavy machinery breaks down unexpectedly, a contractor could spend $30-32,000 for the emergency repair.
As necessary assets that support construction operations, these specialized machines and vehicles can also help fuel a company’s success.
But before that can happen, contractors must know their actual equipment costs in order to bid competitively and win work, and they must track equipment usage to keep their jobs on track. Surprisingly, however, many equipment-intensive contractors do neither.
Establishing a pricing structure for heavy equipment can be difficult because both ownership costs (including depreciation, insurance, taxes, and licenses) and operating costs (such as fuel, maintenance, and wear and tear) must be considered. Yet what may often be even more challenging is how the contractor will collect data on equipment usage from the field and convert it into useful information for the office.
Fortunately, that’s where technology can help. Construction equipment management software makes it easy to track equipment hours and allocate costs to a job for more effective cost management.
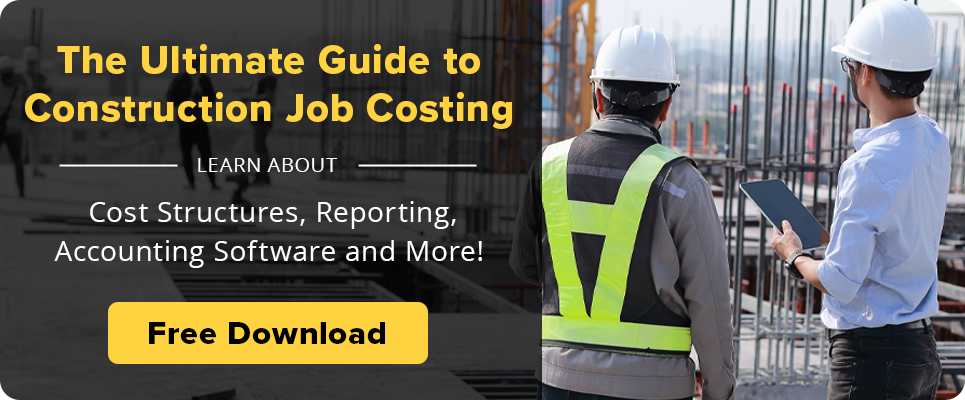
When equipment cost and usage data are combined with accurate labor, material, and subcontractor costs, contractors get a complete job-cost picture for better decision-making and, potentially, greater profits. Tracking equipment hours and costs is usually a three-step process.
Step 1: Establish Equipment Rates.
The best method of pricing a piece of equipment is to use actual costs.
Typically, an internal rental rate can be determined for each piece of equipment by dividing the original cost of the equipment by the estimated years of useful life. Added to this cost are estimated annual repair costs, estimated annual insurance and tax expenses, and any other costs that may apply.
The resulting total is then divided by the estimated annual hours of utilization to arrive at the equipment’s estimated standard hourly rate.
In reality, this method may not work as a good starting point for most contractors because unless a contractor has already captured historical data on all equipment costs, the numbers just aren’t available.
In that case, contractors can turn to equipment rate manuals, such as the Rental Rate Blue Book, which provides step-by-step instructions on how to determine an appropriate rate.
Step 2: Gather Actual Equipment Hours From the Field.
By far, the most effective way to gather heavy equipment hours on a job is to include this information on field workers’ timecards.
For example, Joe Smith’s timecard might show that he worked eight hours on Job #20, under the site-prep cost code, using bulldozer #1. Efficient as this method may be, many contractors struggle to get the proper job and cost code information from their field workers, let alone which pieces of equipment were used.
As a result, contractors often have to settle for other methods, such as gathering daily or weekly equipment timesheets. Although this requires a separate step for data entry and the information is not as detailed, the contractor is at least able to capture the construction equipment usage cost by job and cost code.
FOUNDATION®’s construction time tracking software work together to make accurate equipment-usage records from the field a regular function of employees logging their time.
For an even clearer picture of equipment costs and to help with fleet management, contractors should also track the idle time and downtime for equipment allocated to a job.
The formulas used to calculate these costs are typically a percentage of the equipment rate in order to account for the lack of wear and tear on the equipment. This data is crucial because it allows contractors to help make certain that equipment dedicated to a job is, in fact, being used and providing revenue for that job.
Step 3: Enter Equipment Hours.
Once equipment rates have been established and the usage hours have been gathered, the next step is to get the data into the accounting system where, hopefully, job-cost reports, including heavy equipment costs, are automatically updated.
Unfortunately, another roadblock to construction equipment costing comes into play if a contractor’s accounting system is not able to track or calculate equipment costs.
To track these costs, small business and general-purpose accounting software users must rely on spreadsheets or other external applications. Because this additional process takes so much time and the information is often unreliable or outdated, many contractors may decide it’s not worth the effort.
For that reason, construction accounting systems should have even greater appeal to contractors. With fully integrated job-cost accounting software like FOUNDATION, equipment costs enter the system (from payroll timecards, for example) and automatically update both the equipment module and job costing.
Many systems also provide integrated mobile applications, such as FOUNDATION mobile time tracking software, that allows contractors to eliminate extra data entry and streamline the process. To help save time and reduce data-entry errors even further, users can define multiple costing rates and set defaults for each piece of equipment.
Equipment Management Benefits of Technology
In addition to allocating equipment costs to jobs, FOUNDATION offers numerous benefits to contractors when it comes to equipment management. It enables users to record, store, and easily access equipment information, including,
- Licenses
- Serial and Model Numbers
- Purchase Dates
- And Prices
Construction companies can track full operating expenses for each piece of equipment, such as fuel usage, insurance, labor hours, repair costs, and other details.
Another valuable feature is scheduled maintenance. Based on user-defined criteria like hours of use, odometer readings, or time frames, FOUNDATION will automatically generate both service and maintenance work orders.
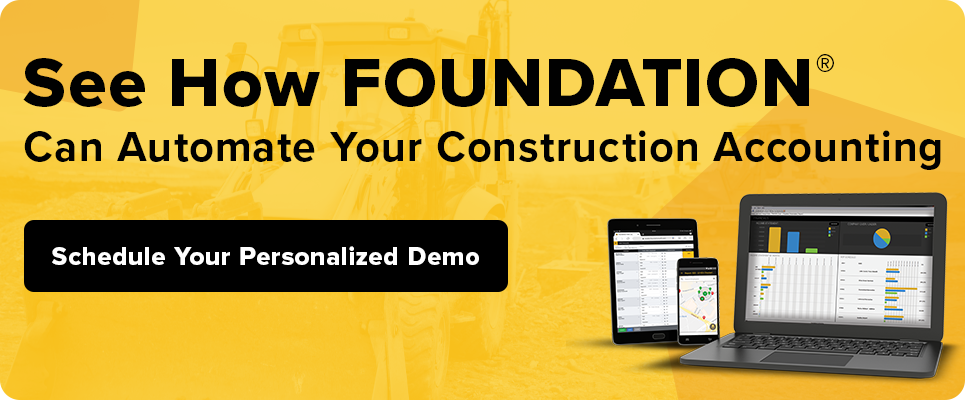
Without question, equipment-intensive construction is a data-intensive business. Tracking equipment hours and costs to jobs belongs to the “get work, do work” cycle that drives a contractor’s business.
Having historical data on equipment usage and costs is absolutely necessary for creating accurate and competitive bids (“get work”) and knowing the full, detailed data picture improves the decision-making and efficiency that keep businesses competitive (“do work”).
Considering this, contractors can ill-afford to neglect equipment costs and usage, especially when construction technology exists to simplify this critical aspect of their business.
Foundation’s Construction Equipment Management Software, specifically, offers all of the functionality required to ensure that your equipment is helping to drive your success.
*A version of this article first appeared in Modern Contractor Solutions.
Share Article
Keep on current news in the construction industry. Subscribe to free eNews!
Our Top 3 YouTube Videos
Learn about our software more in depth with product overviews, demos, and much more!
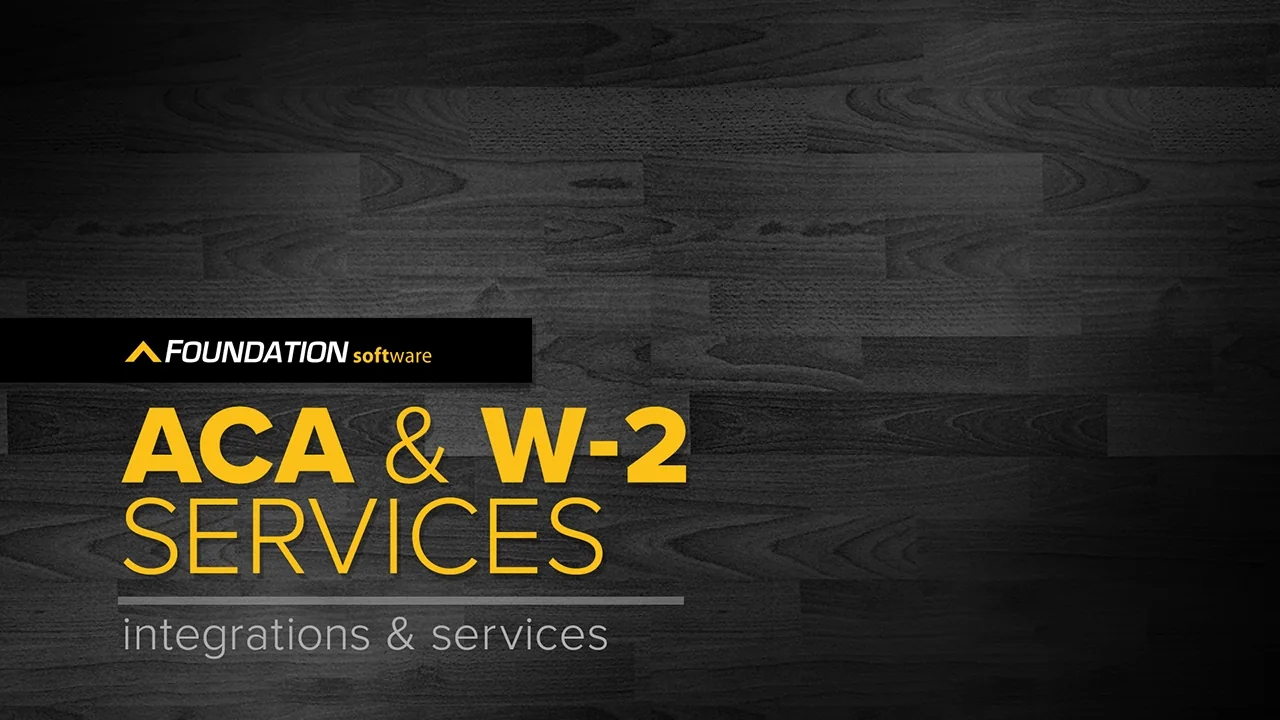
Our ACA reporting & e-filing services include official 1094-C and 1095-C IRS reporting, optional e-filing (no applying for a TCC code required), mailing to your employees and experienced support to help you.
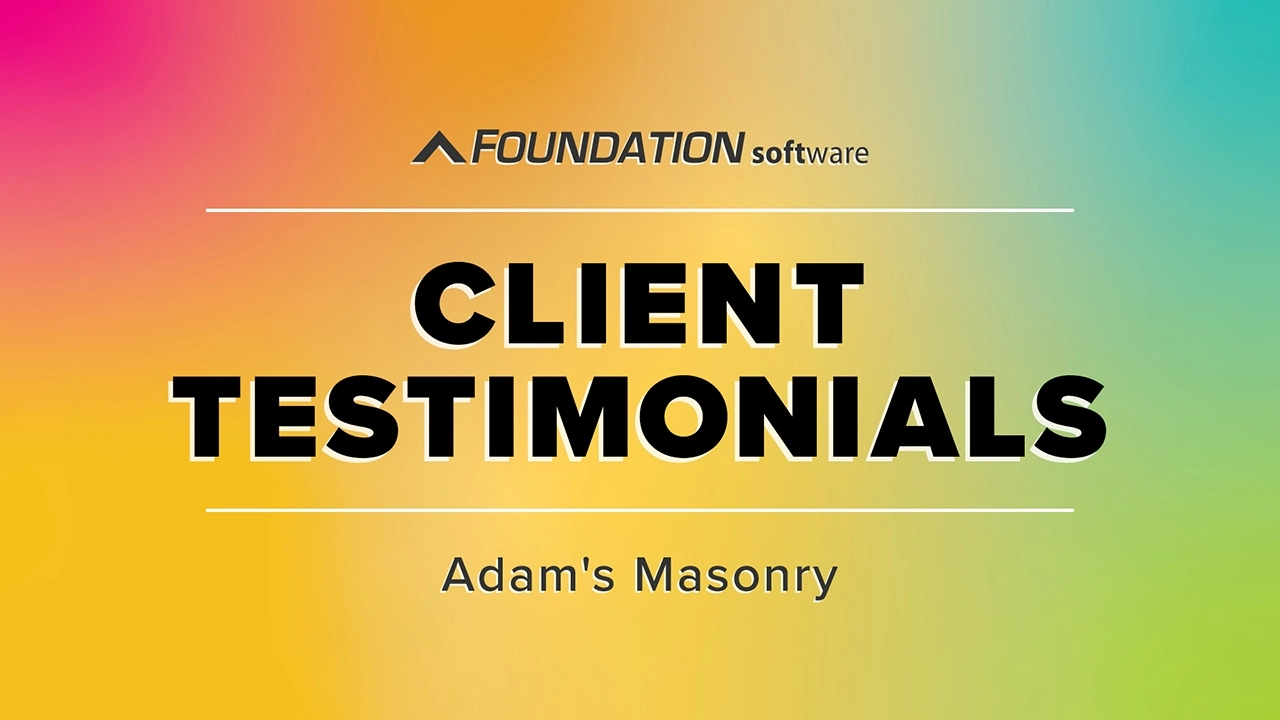
There are plenty of reasons to make FOUNDATION your choice for job cost accounting and construction management software — just ask our clients!
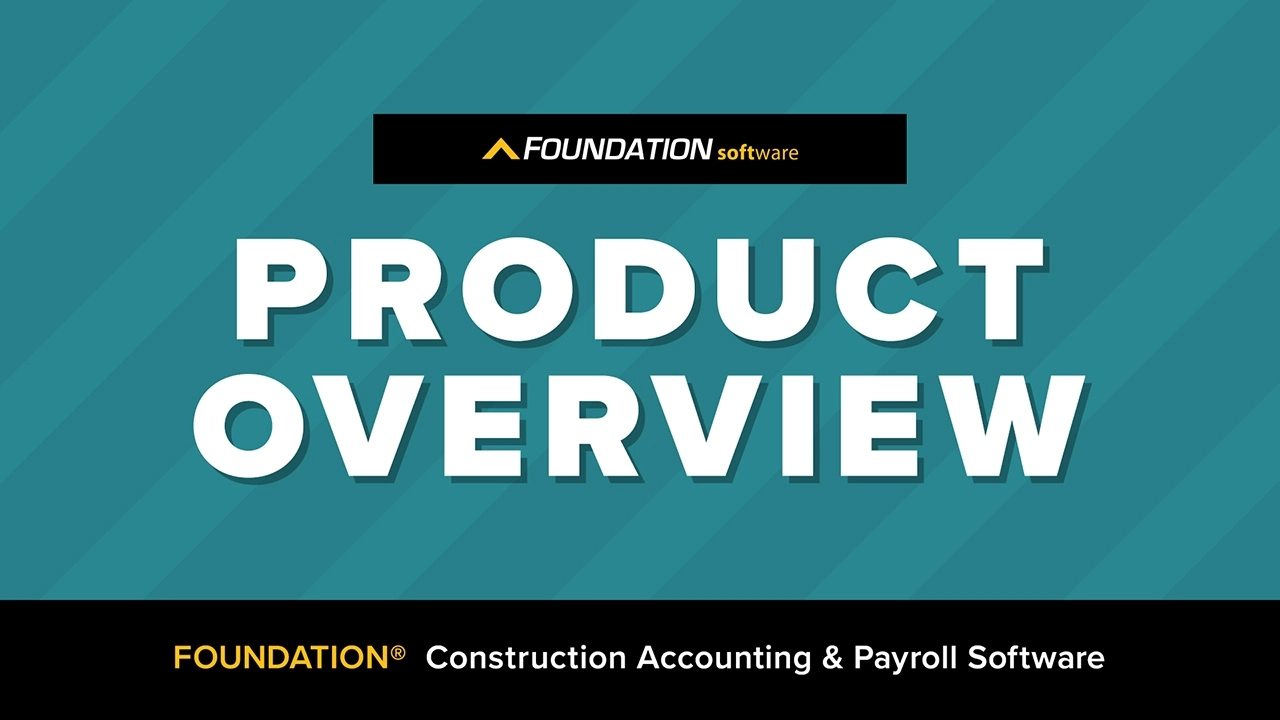
From job cost accounting software, to construction-specific payroll. Get an overview on your next all-in-one back-office solution.